When sustainability destroys the process
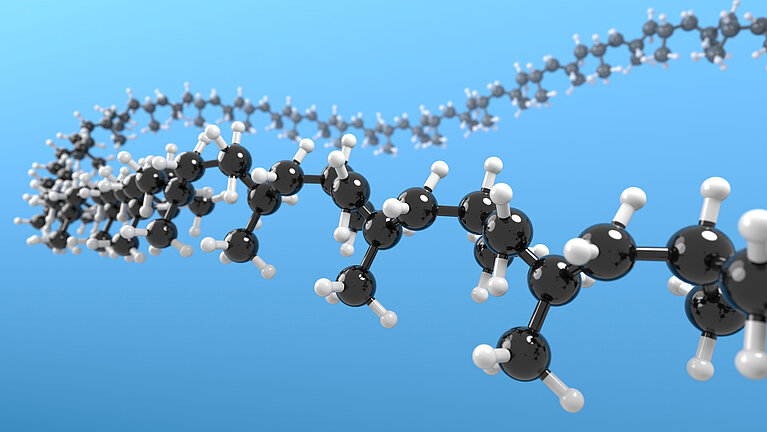
Using environmentally friendly plastics for medical applications
The medical industry is increasingly switching from polyvinyl chloride (PVC) to thermoplastic elastomers (TPE). This trend is motivated by several factors. One major reason is health and environmental protection.
The advantages of TPE for medical applications:
TPE does not contain phthalates and is therefore safer for medical applications. It is less likely to cause allergic reactions or inflammation, making it ideal for use in medical devices. TPE is also easier to recycle and has less impact on the environment by avoiding toxic substances during production and disposal. The flexibility and adaptability of TPE offer additional benefits as it can be easily customized to meet specific requirements while offering high durability and resilience. Stricter regulatory requirements regarding harmful chemicals are also encouraging the switch to TPE as a safer material alternative.
The difference between PVC and TPE:
PVC and TPE differ fundamentally in their chemical composition. At the same time, they also have similar physical properties, which simplify the switch. PVC is produced by polymerizing vinyl chloride, a toxic and carcinogenic monomer. This process requires additional substances such as plasticizers and stabilizers, which often contain heavy metals. In contrast, TPE is produced by combining plastic and rubber in a thermoplastic process that is less harmful to the environment and does not require toxic chemicals.PVC is robust, chemically resistant and inexpensive, but is made flexible by the addition of phthalates, which poses health risks. TPE, on the other hand, is naturally flexible, requires no plasticizers and is more biocompatible.
The disposal of PVC also poses a major problem, as hazardous chemicals such as dioxins are released during incineration. These are highly toxic and harmful to the environment. TPE, on the other hand, is easier to recycle. It can be melted down and reused without significant material degradation, which reduces the environmental impact.
The right joining process for TPE:
When joining TPE components, the focus is particularly on the smooth surface structure of the material. Bonding TPE requires special adhesives that are chemically compatible with the material and offer sufficient elasticity. However, these special adhesives are often more expensive and more difficult to handle than conventional adhesives. In addition, the surface of TPE components sometimes has to be chemically pre-treated to ensure adhesion, which causes additional production steps and costs.
Hot welding of TPE requires precise temperature control and special equipment, as the material can be damaged if the wrong temperature is used. The smooth surface of TPE also makes it difficult to form stable joints, as the melting properties of the material are less predictable than with PVC.
A particularly effective solution to these challenges is ultrasonic welding. This method uses high-frequency sound waves to heat and fuse the joints. Ultrasonic welding is fast, efficient and creates strong, durable joints without the use of adhesives. The precise application of energy enables controlled and uniform fusion of the TPE components, resulting in high-quality joints. In addition, this technology minimizes material changes and ensures consistent quality of the end products.
Change and increase product quality:
The switch from PVC to TPE in the medical industry is a necessary step to minimize health risks and reduce environmental impact. TPE offers numerous advantages in terms of biocompatibility, durability, production and disposal. Despite the challenges of joining TPE components, there are effective solutions such as ultrasonic welding, which has proven to be particularly beneficial. By using these advanced joining techniques, the quality and safety of medical products can be further improved.
Discover how ultrasonic welding can help optimize the manufacture of your medical products.