Achieve Up to 90% Reduction of Operating Costs in Your Diaper Production
Increase the output of your diaper production while saving up to 90% of your operating costs with ultrasonic bonding! Thanks to strong connections without adhesives, you can manufacture your baby diapers, adult diapers or femcare products more efficiently than ever before.
Benefit from:
- Soft & sustainable connections without additional joining agents
- Significant savings in procurement, transport and storage costs
- Safe bonding process even at the highest production
Learn more about the benefits of ultrasonic bonding for your hygiene products!
Discover Your Hygiene Application
White Paper: Your Guide For Maximum OEE in Diaper Production with Ultrasonic Bonding
Discover in our white paper how you can reduce your operating costs by up to 90% with ultrasonic bonding! With practical examples, you will learn everything you need to know about ultrasonic bonding for applications such as side seam, leg cuff or elastic entrapment.
In our free white paper, we show you:
- How ultrasonic bonding can permanently maximize your output and OEE
- The enormous savings potential offered by ultrasonic bonding
- How sustainability and product quality increase thanks to ultrasonics
Discover the Way to Top-Efficiency in Diaper Manufacturing with Ultrasonics!
Faster Time to Market with the Ultrasonic Laboratory NONWOVENS
In our ultrasonic laboratory, we have the ideal conditions for developing the perfect bonding process for your application. The latest equipment enables us to carry out detailed tests under realistic production conditions, facilitating integration and accelerating time to market.
Benefit from more than 60 years of experience in ultrasonics and get a safe, sustainable and efficient bonding solution for your application!
Partner with Us and Reduce Your Operating Costs
Contact our Nonwovens Team to discover how our premium solutions can increase the output of your diaper production while saving up to 90% of your operating costs. We look forward to hearing from you!
Easy Integration with Us by Your Side
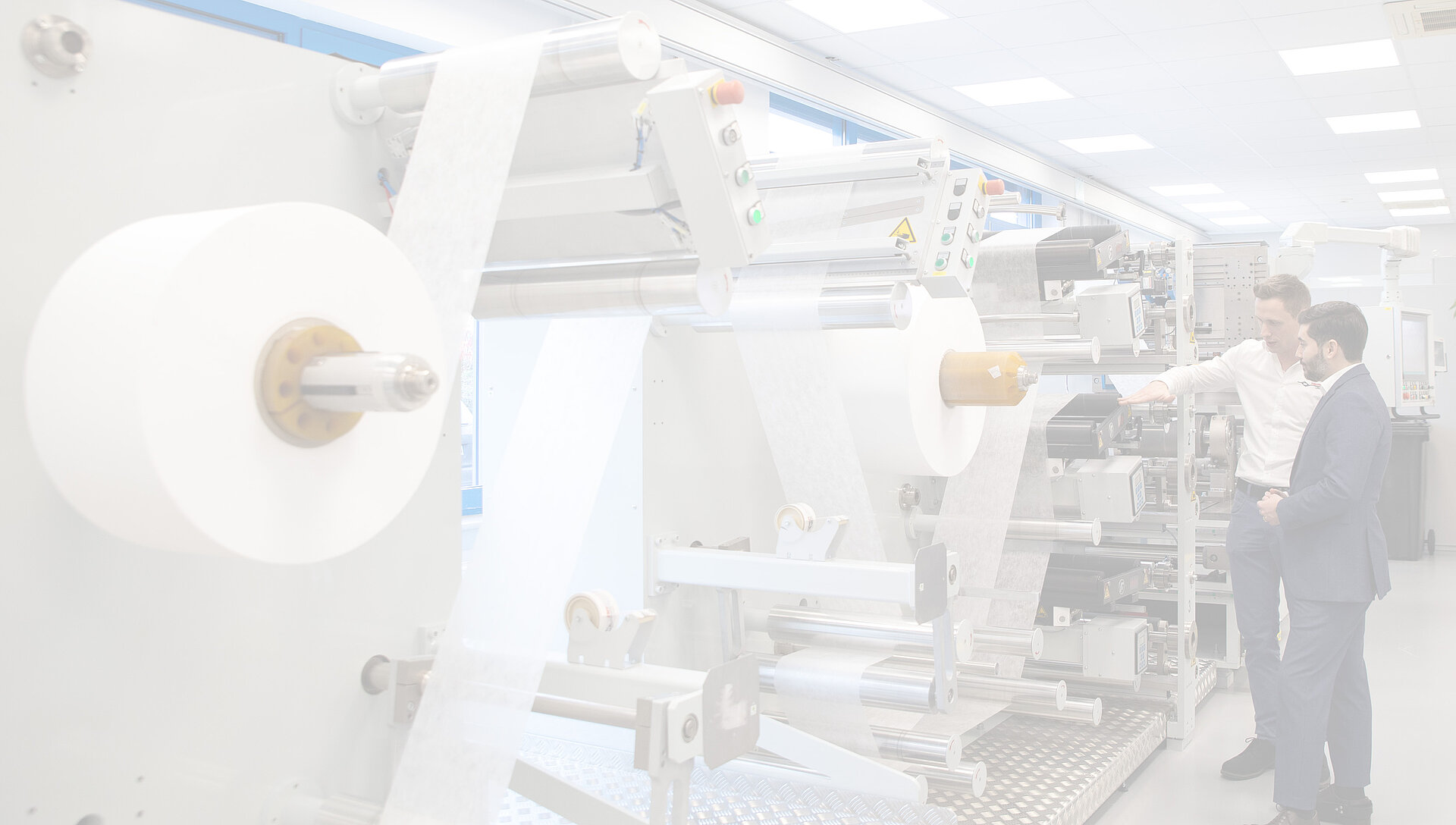
Thanks to our experience in ultrasonic bonding of hygiene products, we work with machine manufacturers all over the world.
Our Trusted Advisors know exactly which steps are necessary to integrate our ultrasonic systems into large or small diaper production lines.
Benefit from:
- Many years of experience in integrating our systems into productions around the world
- Space-saving modules for easy and fast integration
- Global, 24/7 support in your local language
Work with us for a smooth integration of ultrasonic bonding technology into your diaper production!
FAQ – Ultrasonic Bonding for Hygiene Products
As a particularly efficient and reliable process, the connection of nonwoven materials with ultrasonic permanently reduces operational costs in the manufacturing of hygiene articles. This is primarily achieved by:
- Reduction of materials
As ultrasonic bonds nonwoven materials without additional joining agents, enormous amounts of adhesive can be saved here. This not only reduces acquisition costs, but also lowers the costs of storing, transporting and documentation of hazardous materials.
- Reduction of rejects
Modern welding process controllers such as our MICROBOND System G4 enable extremely precise and reliable control of the welding parameters. This ensures that the ideal parameters are permanently reproduced, guaranteeing consistent, outstanding joining results.
In addition, the controller software enables digital quality control in real time. This data can be used to identify error sources immediately, but also to identify long-term potential for process optimization. This reduces rejects in the manufacturing of diapers, sanitary napkins and other hygiene articles to an absolute minimum.
Learn more about the reduction of operating costs in the hygiene industry in our free white paper.
Our space-saving ultrasonic modules can be integrated into new or existing systems, even if an alternative joining technology was used before.
Our experts are always on hand to provide consulting services for the integration of our modules to ensure a quick start-up. Our many years of experience in working with machine builders around the world help us to do this. We value close coordination, reliable adherence to deadlines and fast support in the local language in every phase of our implementation.
This has enabled us to successfully integrate our solutions into numerous large-volume and smaller production systems around the world. Of course, we also offer global support 24/7 after integration to ensure optimum availability and OEE of your production system.
As ultrasonic bonding does not require any additional joining agents such as adhesives for strong connections, the original properties of the material are retained. This means that soft nonwoven material maintains its softness in the finished product.
Even particularly soft materials, such as ATB nonwoven materials, can usually be bonded with ultrasonics. We can evaluate individual compositions of your materials in our ultrasonic laboratories and develop the ideal welding process.
You can also find more information on this in our white paper.
Since our founder, Walter Herrmann, invented the continuous bonding of nonwoven materials with ultrasonics over 30 years ago, we have successfully solved thousands of applications for our customers.
Our application development engineers work on our customers' projects every day in more than 40 ultrasonic laboratories worldwide. This has enabled us to gain enormous experience in dealing with a wide range of applications, materials, and products. As our partner and customer, you benefit from this knowledge, as it enables us to develop processes quickly and reliably.
If ultrasonic bonding is the right solution for your application, we would be happy to demonstrate its potential after conducting initial tests in our ultrasonic laboratory.
Numerous nonwoven material products benefit from ultrasonics. The most common hygiene products include
- Baby diapers (Side Seam / Leg Cuff / Back & Top Sheet / Fastener Tape / Elastic Waist)
- Adult diapers (Side Seam / Leg Cuff / Back & Top Sheet / Elastic Waist)
- Sanitary napkins (Wing Attachment / Textiles Edges / Topsheet and Acquisition Distribution Layer)
- Cosmetic products such as cleaning pads or disposable washing gloves (form welding of nonwoven material / cutting / embossing)
In general, ultrasonic can be used for the following nonwoven materials applications:
- Welding / longitudinal seal
- Welding / cross seal
- Laminating
- Embossing
- Perforating
- Cutting
Discover the perfect ultrasonic solution for your application.
Download Expert Resources
Learn more about the benefits of our ultrasonic bonding technology for your nonwovens application. Our downloads contain knowledge from more than 60 years of ultrasonics, providing valuable insights into advanced assembly techniques. By sharing our technical expertise, we foster a close partnership on equal terms, ensuring we can execute projects as quickly and successfully as possible.
Download our exclusive resources to unlock decades of innovation and stay ahead of the rapidly evolving hygiene products industry.