Welding metals for e-mobility
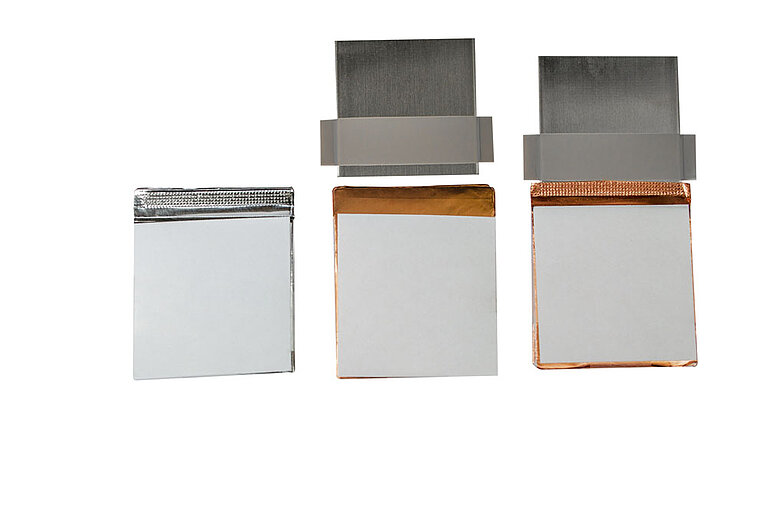
Welding copper and aluminum using ultrasonics
The ultrasonic welding of nonferrous metals is an established process and is currently booming in connection with the growing market for lithium-ion batteries (LIB) – now the main storage source for electromobility. Herrmann Ultraschall has been a specialist in ultrasonic welding for decades and has now developed a new weld system for metals, the HiS VARIO.
Ultrasonic welding is a clean, safe, and environmentally friendly process, which is not only suitable for the pre-welding and main welding for anodes and cathodes in LIB manufacture but also for electrical connections in the automotive, consumer, and electronics industries. The process can be utilized at a manual work station or incorporated automated into production lines. The advantages offered by this process are:
- High strength
- Short weld times
- Low energy consumption
- No consumables
- Longitudinal vibrations break up the oxide layer
Ultrasonic welding is primarily used to join conductive nonferrous and precious metals with copper-aluminum compounds accounting for 90% of the applications. The energy required for joining is supplied by mechanical vibrations. The ultrasonic generator produces electrical oscillations in the 20 or 35 kHz range for this from the 50-Hz mains alternating current. A converter is used to turn the electrical oscillations into mechanical ones in the same frequency. The weld tool, called the sonotrode, transfers the vibrations to the joining partner. The sonotrode couples with the joining part facing it and makes it oscillate longitudinally. The other joining part is held in a structured anvil and does not move. The sonotrode’s coupling surface must also be structured, as otherwise the top joining partner would not move, which is to say no relative motion would be generated.
The oxide coating at the joining sites is broken up by the intensive friction and the two joining parts are fused together with a molecular bond under simultaneous exposure to pressure. The decisive aspect of the welding is not the heat produced, which is far below melting point, but the relative motion of both joining partners. As a result of the low process heat, there is no negative effect on the substance’s material structure. The joining partners’ maximum material thickness is 2 to 3 mm for copper sheet, depending on the weld surface. The power requirement is between 1,000 and 6,200 watts, depending on the application.
Important process visualization
The system control checks the process parameters and visualizes them. This graphical display of parameters on the machine screen, which includes amplitude, energy, weld depth and weld force, is turning out to be an important instrument to ensure process stability. A process window must be determined for each application to balance out material and production tolerances. All the upstream cell production process steps must be taken into account at this stage. It is important to reduce rejects to a minimum, especially in the case of expensive battery cells. When determining the welding parameters, i.e. taking the application, material and production environment into account, it is essential to think holistically. Which is why it is important to get the ultrasonic technology suppliers involved in product development as early as possible. Herrmann Ultraschall sees fine parameterization as offering great opportunities to further improve the production quality and service life of sonotrodes. Correlations can be observed between process stability and particle reduction, and between energy inputs, a stable converter, and the weld tools’ service life.
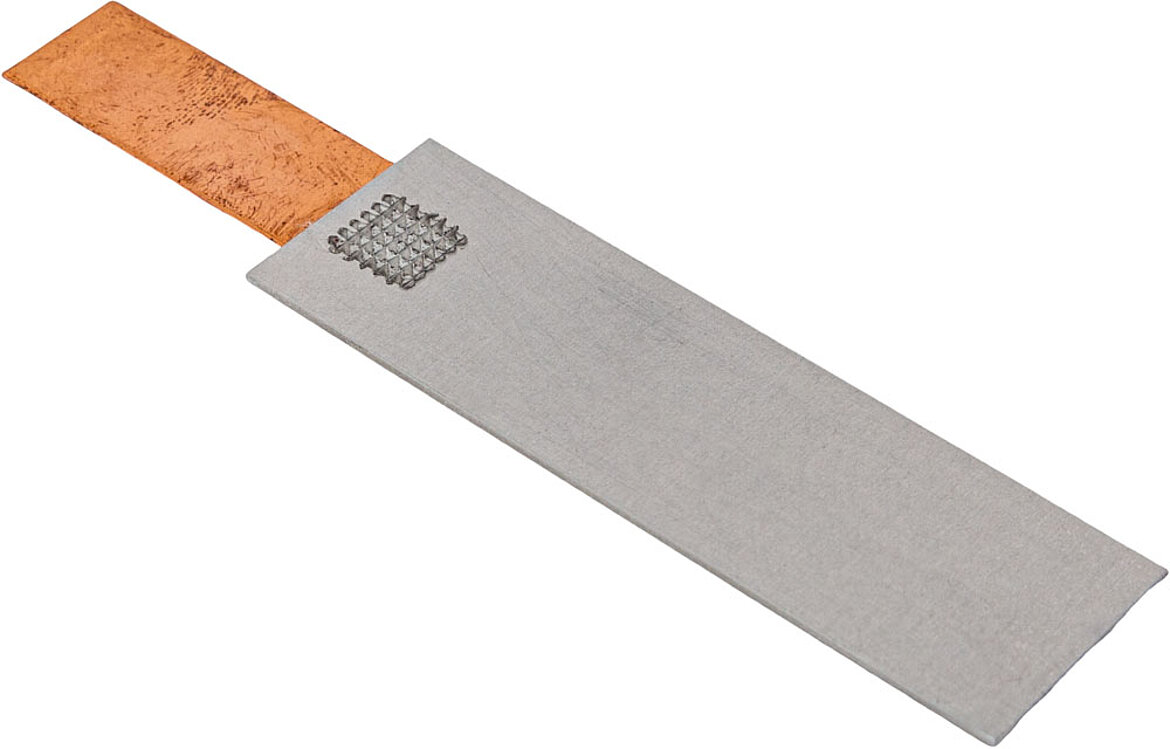
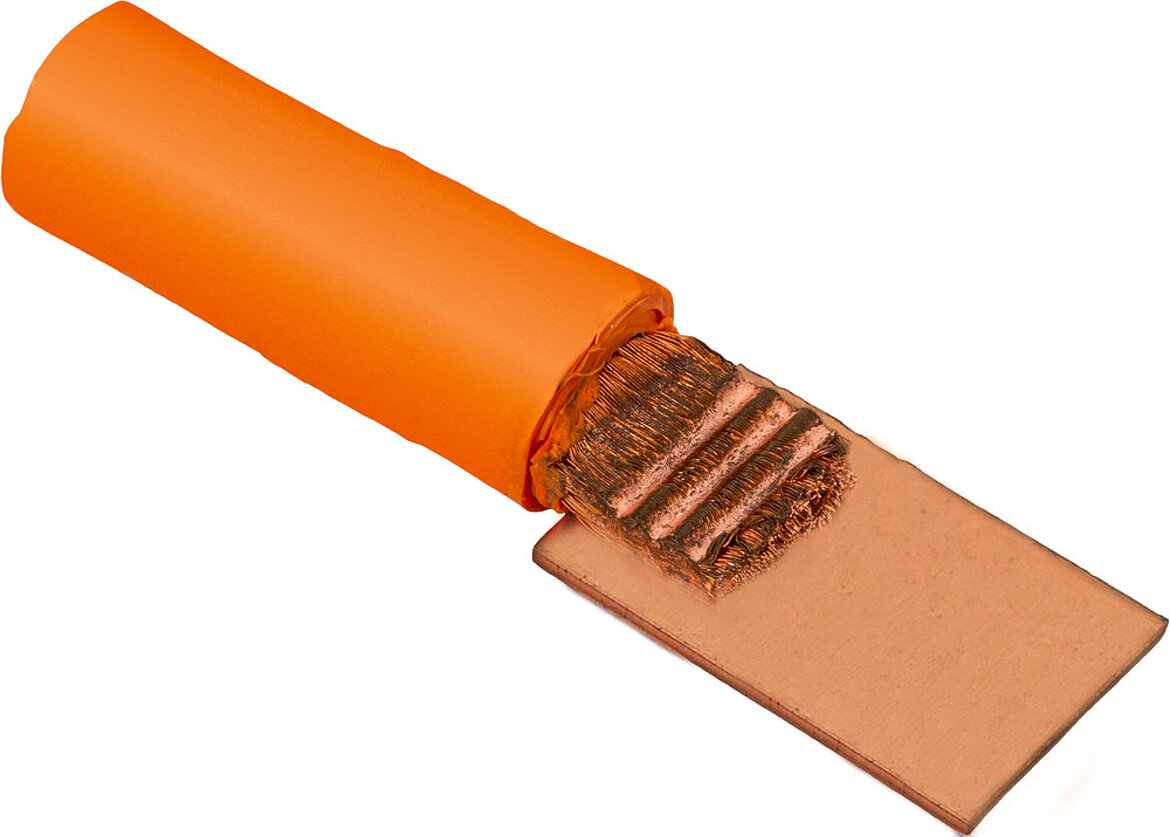
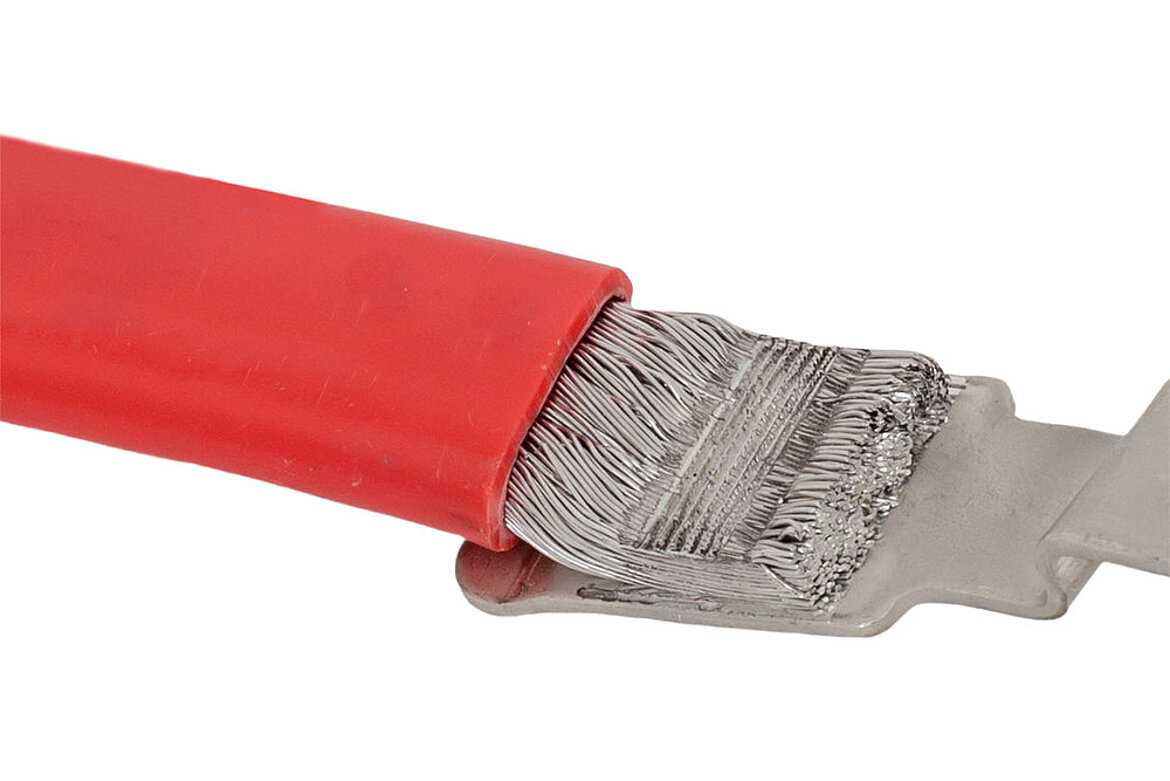
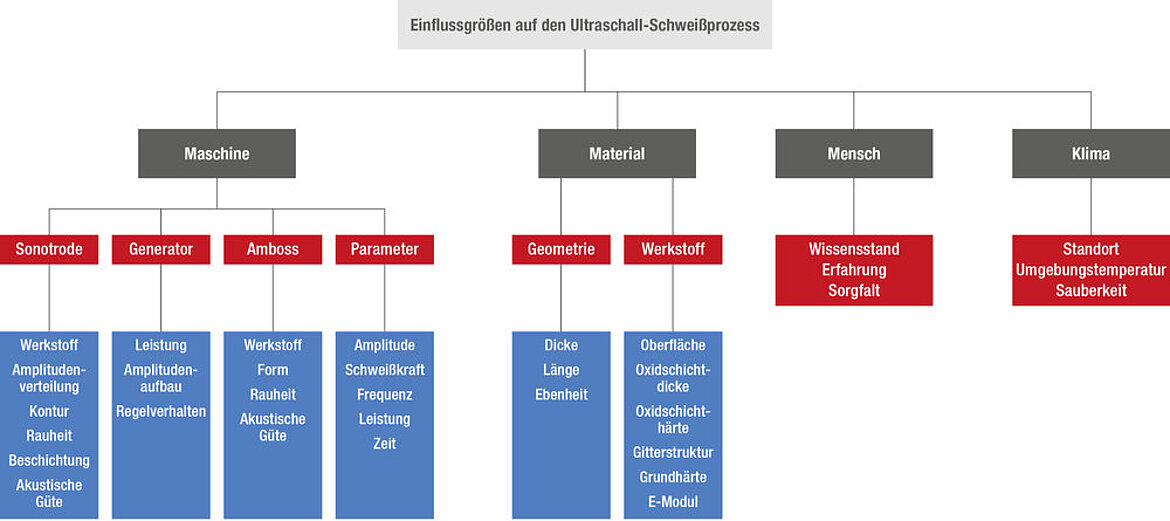