Ultrasonic welding of non-ferrous metals
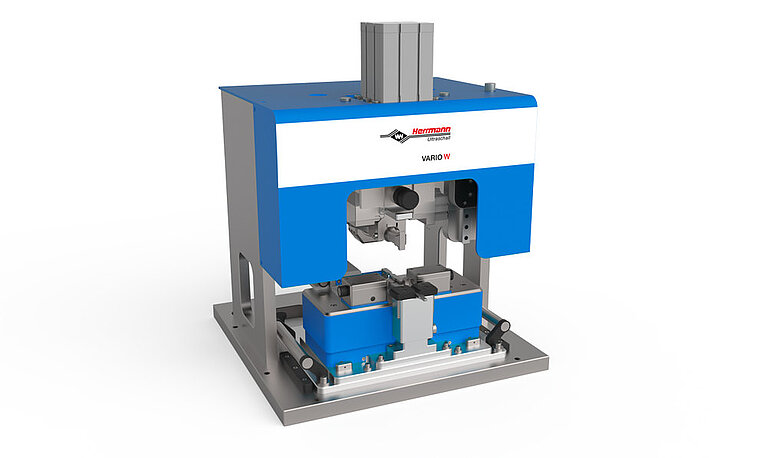
Visualization for a stable process
Ultrasonic welding of non-ferrous metals is a technique used throughout numerous industries, including automotive and electronics. The technology used for this kind of non-ferrous welding works quickly to create permanent bonds while also improving the materials’ electrical conductivity. Ultrasonic welding for copper wire and other non-ferrous metals involves the use of a sonotrode, which uses high-frequency mechanical vibrations to create an oscillating shearing force. The two weldable metals to be joined are held together against the anvil as the sonotrode applies force introduced at right angles to the interface.
The shearing forces created by the vibrations result in a bond between the two metal surfaces, while continued oscillation results in the welding area growing until it reaches the desired bond. These bonds are formed at the atomic level, where the two metals recrystallize into a new structure that has the properties of cold-worked metal. Unlike other forms of joining non-ferrous metals, ultrasonic welding produces bonds that are homogeneous and last much longer. Combined with its ability to increase electrical conductivity, it’s no wonder that ultrasonic welding for copper wire and other components is found commonly in a number of industrial processes.
Herrmann Ultraschall has been a specialist in ultrasonic non-ferrous welding for decades and is presenting its new HiS VARIO welding system for metal welding such as copper and aluminum at Productronica. The system can be used as a manual workstation or automatically integrated into production lines.
When working with weldable metals, the process stability and the life span of the welding tools play a major role. For the process set-up, the application, the types of non-ferrous alloys and the production environment will have to be taken into account. For each application, optimal process parameters and the associated process windows are determined in order to ensure consistently high production quality. Often it is also necessary to compensate for certain material and finishing tolerances.
Display and optimize process graphics via screen
The visualization of the welding process has been a priority at Herrmann Ultraschall for decades. This is the only way to understand, optimize and monitor the joining process. The system control VARIO generates a graphical representation of all relevant process variables such as power, joining distance, force, amplitude and frequency - with a very high resolution of one measured value per millisecond. The curves document the characteristics of the weld process and thus enable parameter optimization. These can then be displayed as reference graphics and used for quality assessment. Herrmann Ultraschall sees great opportunities to finely tune parameters and support process visualization, to further develop the welding quality and the service life of the sonotrodes.
Ultrasonic metal welding basics:
Ultrasonic welding of non-ferrous metals such as copper and aluminum is an established joining technology and is suitable for many electrical connections in the automotive, consumer and electronics industries. In addition to typical terminal and cable connections, the use of ultrasonic welding has also greatly increased in the production of anode and cathode due to the increasing demand for lithium-ion batteries.
The advantages of ultrasonic welding are:
■ High strength
■ Short welding times
■ Low energy consumption
■ No consumables
Herrmann Ultrasonics has the equipment and the know-how to help you with this process. Our range of ultrasonic metal welding machines includes the innovative HiS VARIO system. To learn more, get in touch with us today.
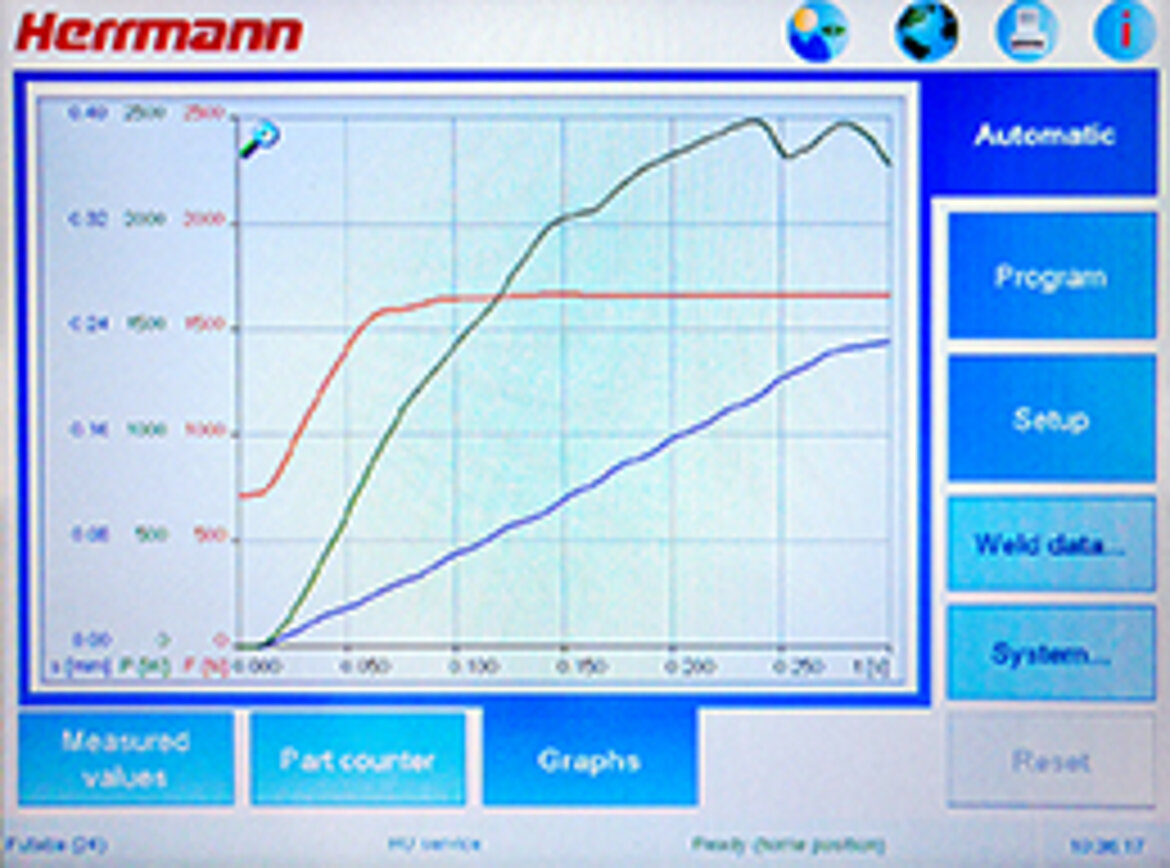
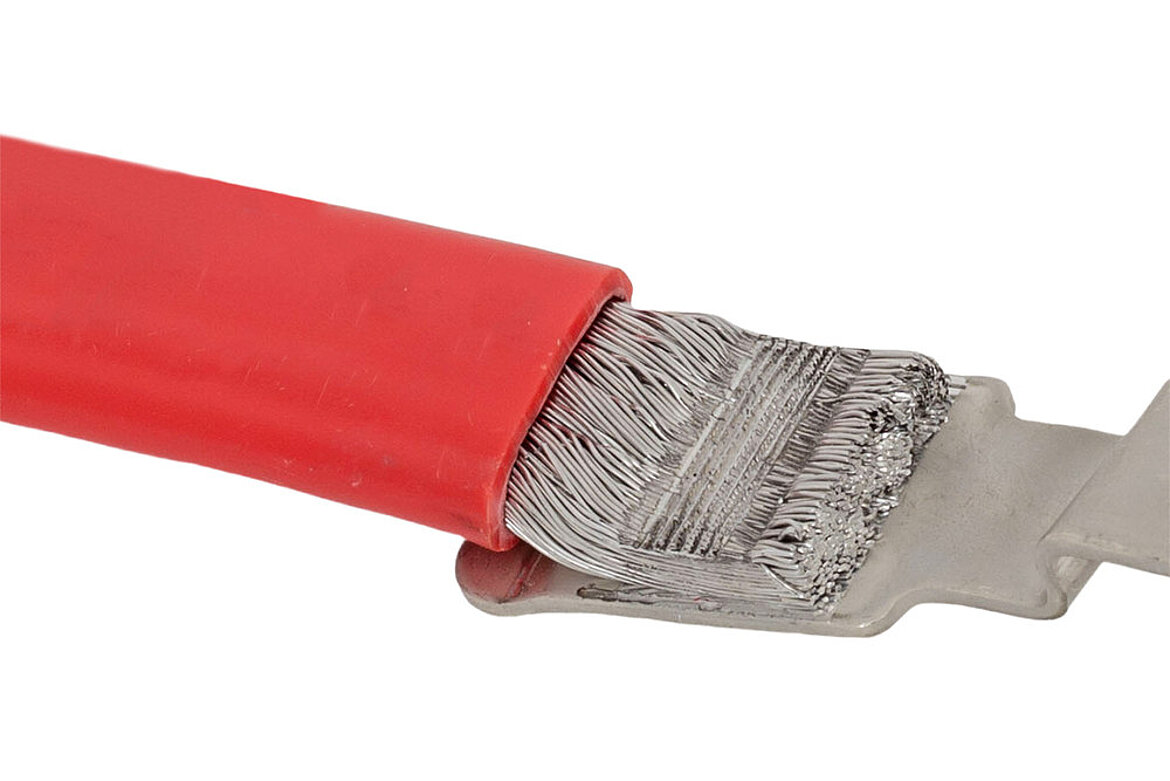