Ultrasonic sealing: Enabling Sustainability
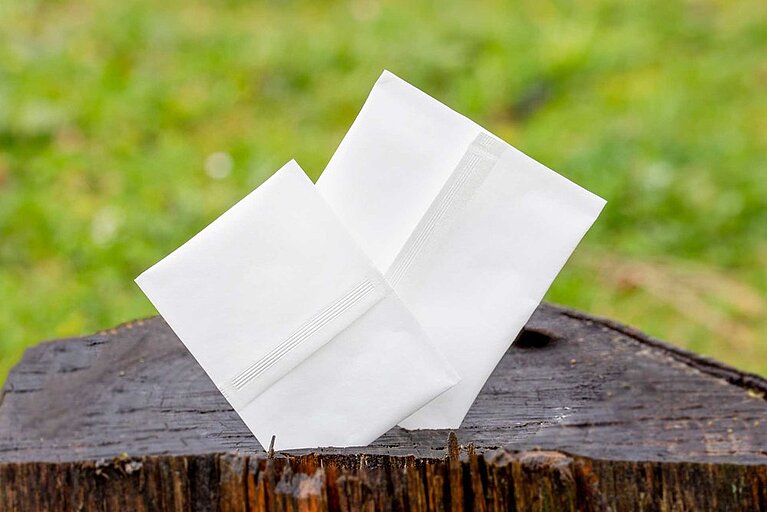
Trend towards mono materials and paper
Mono-materials and paper composites for packaging are increasingly in demand and the number of inquiries regarding new recyclable materials is increasing at the ultrasonic laboratory of Herrmann Ultraschall. Many of the major food companies have set themselves high sustainability targets and are testing the new materials. Next to it, the ultrasonic sealing of cardboard composites with and without aluminum barrier is already a proven process. Bioplastics such as PLA also demonstrate good ultrasonic sealing properties, which is already being applied with coffee capsules.
A starting point for genuine circular economy and an increased recycling rate is single-variety packaging. This means, for example, that films are no longer made of layers of different plastics, but of just one or more layers of a single material. This in turn has consequences for conventional processes such as induction and thermal contact. Induction welding does not work without aluminum, and heat contact processes are generally very limited for paper composites due to their insulating effect.
The advantages of ultrasonic sealing are very beneficial to the current trend towards mono-material packaging. Ultrasonics only generate thermal energy inside the seal area. The support layer is not melted, even though it is made of the same material. This means the amount of energy introduced can be defined very precisely, which is a huge advantage for mono-materials with a tendency to have a smaller process window.
Tighter process limits can be maintained
Robert Hueber, PACKAGING Business Unit Director at Herrmann Ultrasonics: “Ultrasonic technology can also deliver good sealing results with narrow process limits, especially with regard to tightness and visual appearance. The thermal expansion is kept to a minimum. Heat sealing processes can demonstrate disadvantages of excessive heat input, especially in the high-speed welding of film webs made of mono-materials. This can lead to the uncontrolled elongation of the film web and therefore impair the process.”
Mono-materials are also more susceptible to film shrinkage due to mechanically and thermally less stable support layers. The sealing seam appearance can suffer and adhesion is possible. Ultrasonic sealing can counteract due to the cold tools. This in turn has a positive effect on downtimes and the need for wear materials such as high-temperature Teflon tapes. Ultrasonics only need energy during the sealing time, so no high stand-by consumption is necessary as with other thermal sealing processes. The tools are immediately ready for use without having to heat up – another contribution to reducing the burden on the environment.
Good to know
The major difference with ultrasonic sealing: the heat is only generated inside the seal
Ultrasonic sealing has become a real alternative to heat sealing for various applications such as wet food containing proteins and sugary drinks in pouches, as well as salad and powdery products. The difference to conventional sealing using thermal jaws is the way the heat is generated. While in the case of thermal sealing jaws the heat comes from the outside and therefore also heats up and can affect the support layer, in ultrasonic sealing the heat is generated by the ultrasonic vibrations inside the sealing layer. It ensures that the sealing layers bond together at a molecular level before there is any undesirable heat conduction through the entire packaging material. As a result, the packaging can be closed much more gently for the type of packaging and feed material. Shrinkage and possible leakage are minimized.